Transforming Manufacturing in Food & Beverage
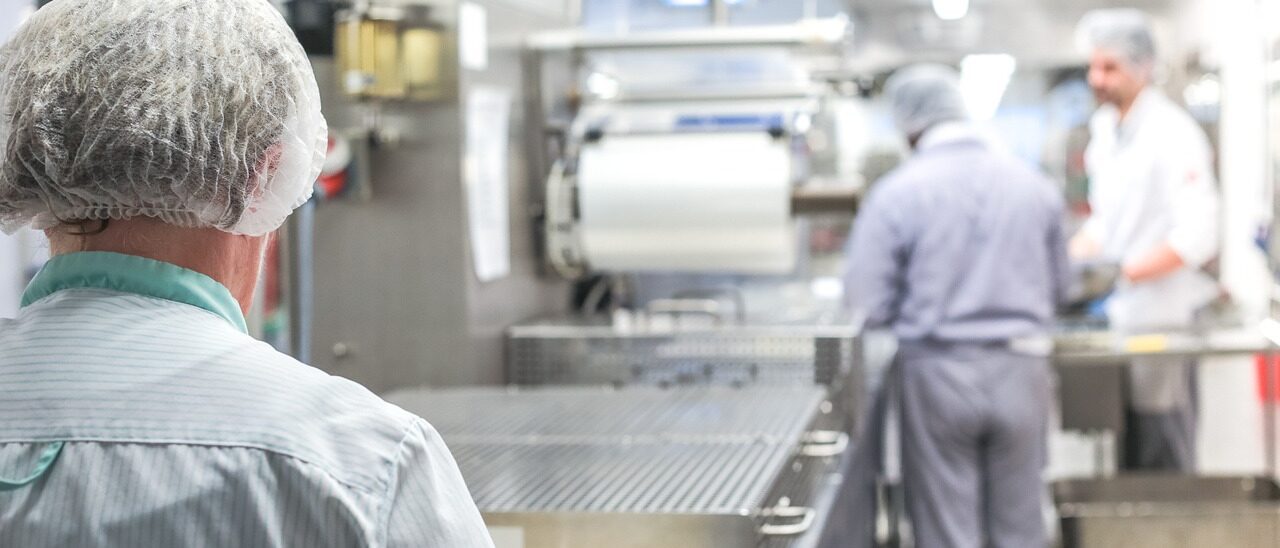
The UK’s food and beverage sector has responded well to the challenges of recent years – not least by bouncing back from the ‘brutal’ losses of 2020, with 2021 exports up on 2020 levels and the forecast for 2022 positive. Investment in staff training, automation and technology, as well as investment in R&D, have created a sector that is the largest within UK manufacturing, larger than automotive and aerospace combined.
Yet too many of the country’s SME food and beverage (F&B) businesses still lag behind when it comes to end-to-end automation and technology adoption. Most have achieved pockets of innovation, both on the shop floor and within administrative functions such as finance and sales. Yet there is a continued disconnect between business areas that is compromising agility and responsiveness as inflationary pressures, as well as global supply chain disruption, take their toll.
Investing in ERP is the obvious step, providing a single, end-to-end solution that can transform productivity, cost control and competitive position – but how can SME F&B manufacturers attain ERP quickly, effectively and at an affordable price point? Don Valentine, Absoft’s Commercial Director and ADIMA ERP Lead explains why a pre-configured ERP solution tailored to meet the specific functionality requirements and cost-effectiveness needs of F&B SMEs is changing the game.
Business Critical Challenges
Soaring raw materials prices and global supply chain disruption are creating huge pressures for a food and drink sector already reeling from Covid-19 lockdowns and an unexpected depletion of the labor force. Indeed, global food commodity prices increased 23% over the past year, fertilizer prices were up 164% and shipping costs rose 226%. Food companies are in widely-reported negotiations – even disputes – with retailers, who are under consumer pressure over the rising cost of living. What proportion of these additional costs can be passed on to the retailer / customer, therefore? How will delays in the supply chain affect the production process – and will that incur penalties from customers if products arrive after the promised date? How will both delay and price rises affect customer and consumer demand?
Traditional business decision-making based on accepted trends in raw materials pricing and customer demand have been thrown into total disarray. Companies cannot rely on last year’s data to make this year’s decisions – that will be a fast track to profit erosion and business loss. But without complete, end-to-end visibility across the entire business, companies are not in a position to make the right decisions at the right time.
And far too many are operating blind, with a mix of different solutions, in different departments; one for finance, one for sales and marketing, for example, another for operations and supply chain. The only way to join up the business processes and decision-making is to painstakingly feed sales demand into production, replenishment, procurement and distribution processes – something that few companies have the time or resources to achieve.
Fast Tracking ERP Deployment
This current set of financial and operational challenges is just one more reason to make the leap to a single, end-to-end, ERP solution that provides complete, accurate and real-time visibility of the entire operation. To be fair, most F&B companies recognize the value of ERP systems, such as SAP S/4HANA, which provide a single source of business information, support process automation and transform efficiency.
SME F&B manufacturers are, however, understandably concerned about the cost and disruption associated with traditional ERP deployment. Designed to support every type of organization from banking to defence, logistics to public sector, traditional ERP solutions need to be so feature rich and offer so many options that they can end up being all things to all men – rendering the initial process of determining the functionality required and the workflows daunting, at the very least.
Which is where the out-of-the-box, preconfigured solution designed specifically to meet the needs of the food and drink sector changes the game. With this approach, the ERP solution is preconfigured up front, delivering the core features and functions required by manufacturers while eradicating the time-consuming and expensive configuration process. As a result, implementation timeframes can be radically reduced – rather than a 12-month project, the full ERP solution can be in place within a 12-16 week period. With the option of cloud-based deployment, F&B manufacturers can move away from the complexity and resource demands associated with on-premise systems, further releasing both cash and in-house resources.
Transforming Competitive Position
With a single ERP solution, a manufacturer can gain immediate control over the entire business process and focus on the core areas of business pain. If just-in-time stock management is the priority, purchase decisions can be automatically driven by real-time sales demand, reducing the risk of excessive, expensive inventory levels and raw material stockpiles. If the goal is to mitigate the risk of spiraling raw materials, combining sales demand with information about materials costs and delivery timescales will enable informed timely purchasing decisions.
Plus, of course, with complete visibility of the entire process, vendor / supplier management will improve. Finance will not inadvertently pay for delayed deliveries, and any potential impact on manufacturing caused by supply chain problems can be assessed and immediately shared with customers. Indeed the entire customer interaction is transformed. Arming the sales team with real-time information on desktop, tablets or mobiles provides immediate access to customer history, what is on order, when it is due, inventory levels at customer distribution centres, credit status and invoice position. Sales staff are empowered to make intelligent, achievable customer offers, without the risk of discounts that could compromise the bottom line – a position that delivers a tangible competitive advantage.
Linking the operational production systems with the ERP optimizes the entire manufacturing process. Sales orders are automatically converted into production orders, which then drives just-in-time stock management on the shop floor. All of which is visible at a glance by staff – either on a mobile device or workstation. This reduces the frustration of chasing instructions and increases the time spent on expert activities, from ensuring contingency in raw material procurement, recipe management across multiple factories / production sites, sampling elements and checking quality, boosting morale throughout the company.
Conclusion
Despite an overall industry investment of £4bn in 2021, an 8% increase on 2020, many F&B businesses post-pandemic are still relying on ageing legacy systems and spreadsheets to get tasks done, believing this inflexible, often out-of-date, disconnected data is sufficient to support corporate decision making.
Yet, with labour shortages and mass economic inflationary pressures adding to the challenges facing SME food and drink manufacturers, the pressure is now on to gain control – and that means better information to support vital decisions, more efficient processes and a way of optimizing staff time and satisfaction. ERP is no longer out of reach for businesses of any size. With minimal up-front costs, an Opex rather than Capex investment model, a cloud-based, preconfigured ERP solution provides rapid access to the automation and business information manufacturers require, fast.