Manufacturing and the power of prediction: an end to unjustified and reactive maintenance.
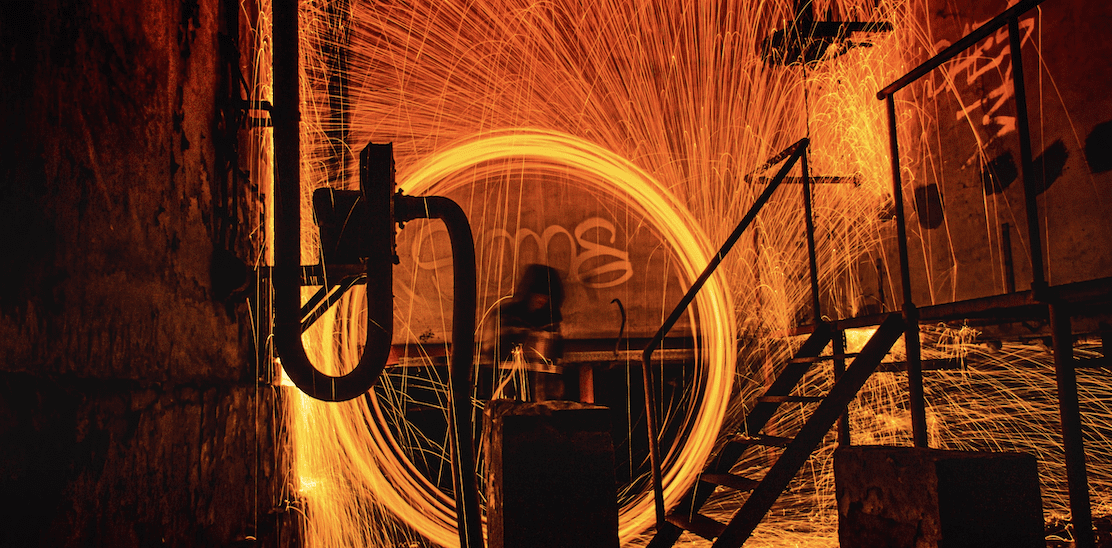
The Industrial Internet of Things (IIoT) is alive and kicking. It is transforming traditional, linear production processes into dynamic interconnected systems across the manufacturing landscape. It’s making its presence felt in production efficiencies, QA process improvements and real-time AI-based decision making. However, there is one area where it still has room to grow. That’s predictive maintenance, giving technicians the power to service networked machinery before it fails.
An end to unjustified and reactive maintenance.
Prevent, correct or predict?
When it comes to maintenance, there are three options available.
Preventative maintenance is performed at fixed intervals. Whether that’s after a certain number of machine hours or at set points within the manufacturing year. It’s all about creating a schedule of repair that kicks in before machinery fails. Even if something is fully working, with no issues, preventative maintenance is still carried out.
Corrective maintenance takes the opposite approach. Machinery is repaired only when a failure has already occurred and the damaged equipment has to be overhauled. Although this strategy saves businesses from purchasing and installing new parts unnecessarily, it can also create production bottlenecks and cause major downtime issues.
But everything becomes more methodical when IoT technologies are available to address issues, alleviate problems and improve processes. That’s when predictive maintenance can be used to assess factory systems and pinpoint the machines that actually require repairs.
It’s an ideal balance. Maintenance is carried out before the point of failure, but not too early, when a part is still functioning correctly and delivering benefit. With predictive maintenance, you’re fixing problems before they start, just as components reach the end of their serviceable lifespan.
The nuts and bolts of predictive maintenance
Predictive maintenance can be overlaid onto a manufacturing plant’s existing IoT installation. All those endpoints, low latency connections and automation subroutines, deployed to streamline production. They can be paired with machine learning and predictive analytics to spot patterns in current and historical data. Whether it’s data from temperature sensors, valves, vibrations or viscosity, all this real-time operational information can predict when an asset or piece of machinery needs repairs, before breaking down completely. You’re only a small step away from proactively identifying the warning signs of mechanical failure and taking timely action.
Practical examples of predictive maintanence
There are a number of ways that sensors can be used to usher predictive maintenance into a manufacturing facility. For example, worn components often radiate more heat than they would
under normal operating conditions. Using infrared cameras, equipment hot spots can be identified automatically and flagged to maintenance crews. As an addition, machine learning could be used to automatically order a new part once a temperature threshold is reached.
Furthermore, acoustic sensors can be used to detect gas, liquid or vacuum leaks in equipment. The same sensors can also detect friction patterns in machinery, with acoustic characteristics changing over time due to worn or poorly lubricated bearings and housings.
Then there’s vibration analysis, allowing plant operatives to determine whether a machine is operating under optimal conditions, based on its vibration pattern. This will often change as components wear out and vibration frequencies change.
For many manufacturers, all these predictive maintenance techniques sit harmoniously alongside existing IoT initiatives. Being able to analyze the condition of equipment on an ongoing basis and foresee potential failures, has to be one of the most natural and effective IIoT progressions.
Making successful implementation plans
So, where do you start? And how can your business adopt these powerful maintenance procedures? Well, here are three things you need to bear in mind as you build out your predictive maintenance capabilities.
1. No more manual data collection
Manual inspections have got to go. These are inefficient ways of tracking the health of equipment and machinery. Industry 4.0 is all about augmenting your teams with connected sensors and smart tools that make it possible to identify potential problems faster and more reliably. Leave the data collection and preliminary error detection to your IoT endpoint network. You should be diverting your engineers’ time into more beneficial, bigger-picture assignments.
2. It’s time to embrace Big Data
You’re going to accumulate data very quickly. Lots of it. And it’s easy for managers to get overwhelmed. But don’t try to interpret the data yourself. There are plenty of analytics platforms out there that can process your data for you. With the right platform you can use machine learning to bridge the gap between your incoming performance metrics and the maintenance that’s required.
So, don’t worry about the data. Once you step back and let your analytics solution do its thing, you’ll be able to focus solely on the key pieces of information that matter.
3. Put cellular into the equation
IoT is built on connectivity. Get this right and everything else begins to fall into place. Get it wrong, and you’re trading seamless, actionable data communications for limited insights and cybersecurity vulnerabilities.
Hard-wired or Wi-Fi connections may work in some settings, but most of the time cellular connectivity is absolutely essential. It’s flexible, resilient, dependable and fast, outperforming the limitations of older connectivity models. When your goal is to stay IoT connected, no matter the circumstances, cloud-native cellular connectivity is your best option by far.
An easier future for manufacturing
As the IIoT continues to pervade factories across the UK, manufacturers are able to make radical improvements to traditional production processes. When the flow of materials, components and finished products is being tracked by sensors, and autonomous machines are alleviating production line pressures, introducing predictive maintenance into the mix is a natural next step. Is your business ready to explore the financial, productivity and efficiency benefits of predictive maintenance?