Increase productivity and innovation with additive manufacturing in the automotive industry
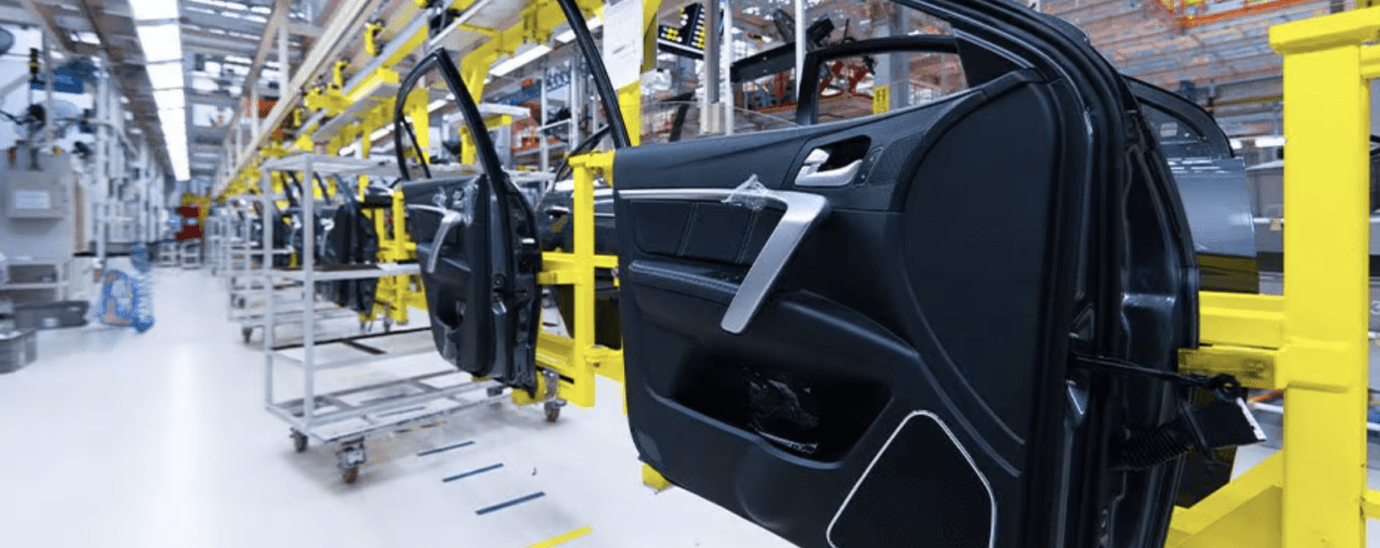
Advancements in 3D Systems’ additive technology has cultivated new possibilities to meet the most urgent challenges in today’s automotive industry. With a combination of innovative solutions and manufacturing productivity, 3D Systems gives consumers a competitive advantage with additive manufacturing (AM).
3D Systems push the boundaries by being the first in delivering and offering manufacturers the fastest solutions available to industries, including automotive. 3D Systems creates bespoke solutions for their customer journey that enables the delivery of high-quality applications.
3D Systems has been leading AM innovation ever since they launched the 3D printing industry in 1986, and is now headquartered out of Rock Hill, South Carolina, with offices, manufacturing facilities, and Customer Innovation Centers around the globe.
3D Systems’ application-focused approach to solving the most difficult designs, and production challenges combines their solutions, expertise, and innovation. As a result, 3D Systems users defy conventional manufacturing limitations and maximize the value of AM.
Innovation while maintaining higher-margins
Innovation without productivity is unrealistic for most manufacturers. While productivity without innovation can lead to low margins, and economic pressures to evolve. Therefore, success in today’s rapid changing automotive industry, demands constant innovation alongside greater productivity. For automotive manufacturers, relying on traditional manufacturing processes can be a bottleneck to innovation and production. Consequently, this requires the development of transformative applications capable of incorporating the latest engineering, and design approaches, to optimize performance and gain a competitive advantage.
The next generation of automotive experiences calls for manufacturers to build vehicles with more personalized connections to consumers. In addition, this may include customized interiors and exteriors or other specialized components. Although doing this with traditional methods can be prohibitively expensive, additive technology gives manufacturers the ability to economically increase the production of tailored products.
3D Systems on Automotive solutions
Automotive manufacturers must be able to design, test, iterate, and produce parts, and components that optimize performance. This needs to be done while applying higher productivity solutions that leverage lean manufacturing, which requires solutions capable of advancing both productivity and innovation.
As such, companies can leverage AM to address key challenges like surface experience, lean manufacturing, robust components, and newly engineered systems. Each of these challenges requires advancements in both productivity and innovation, delivered by advancements in additive technology and automotive applications.
Key challenges for AM
3D Systems AM solutions for body interiors and exteriors give you more control over both performance and visual experience, whilst simplifying and tailoring production. It allows for fast production of Class A surfaces, that deliver customer automotive experiences for specified users or groups. Advancing productivity can mean raising production levels to the hundreds of thousands, or efficient production of components.
With 3D Systems comprehensive portfolio of AM technologies and materials, you can quickly design, test, and iterate custom high-end experiences. Not only can you get precise control over every sensory factor, but you can also reduce overall components to optimize manufacturing.
3D Systems AM solutions allow you to build parts in hours so you can repeat, optimize, and produce your designs. High-performance materials, from rigid plastics to composites, as well as a range of different surface types, make it possible to further maximize style and performance without affecting productivity.
Similarly, often creating tools and components with traditional manufacturing methods that meet innovation requirements, comes at the cost of either reduced quality or productivity. With this in mind, by increasing flexibility and configurability of existing production processes, shorten lead time and raised productivity can be delivered. Thus, whether you are producing complex metal components or custom manufacturing aids,
3D Systems additive solutions can reduce lead times and increase flexibility without sacrificing quality.
3D Systems metal durable tooling significantly improve the quality and efficiency of durable tools. It allows you to leverage a comprehensive set of AM solutions to incorporate innovations like complex dye inserts and high-productivity conformal cooling. Likewise, thier AM technology lets you efficiently tailor jigs, grippers, and other components, and rapidly iterate 3D Systems design while advanced materials help you maintain quality over the long-term.
Many automotive components have to perform within challenging environmental conditions. This includes constrained packaging or prolonged exposure to heat or chemicals. However, performance can be improved by leveraging design freedom that enables greater functional density, utilizing advanced materials that perform over time, and capitalizing on more productive AM platforms.
3D Systems empowers the application of robust components through AM in challenging, packaged-constrained environments. This includes Underhood and Powertrain design components, that maximize both functional and environmental performance. With 3D Systems comprehensive AM solutions, you can consolidate functionality into constrained spaces, while 3D Systems advanced materials let you optimize performance and reduce part counts for more efficient manufacturing.
The advances in automotive architectures and systems are introducing new engineering challenges, which require the development of newly engineered systems. 3D Systems’ AM solutions enable true digital twins, in iteration and validation. Giving unconstrained engineering optimal performance. As a result, leveraging advanced materials such as, energy and fluid management as well as air, and fluid handling. This unlocks design freedom to rapidly iterate, optimize and produce new and innovative components.
In conclusion,
In order to stay competitive in today’s automotive industry, manufacturers need to develop transformative applications that help them stand out. Simultaneously, this needs to be increasing productivity to meet customer demand and maintain their ROI. Both pieces of the puzzle are necessary for success and the right tools. AM enables automotive manufacturers to combine high-value, transformative applications with high levels of productivity. Enabling the production of innovative parts, while maintaining higher margins. Download the ebook here to learn more about how and what AM can be used for.