Transforming manufacturing operations through the use of cobots
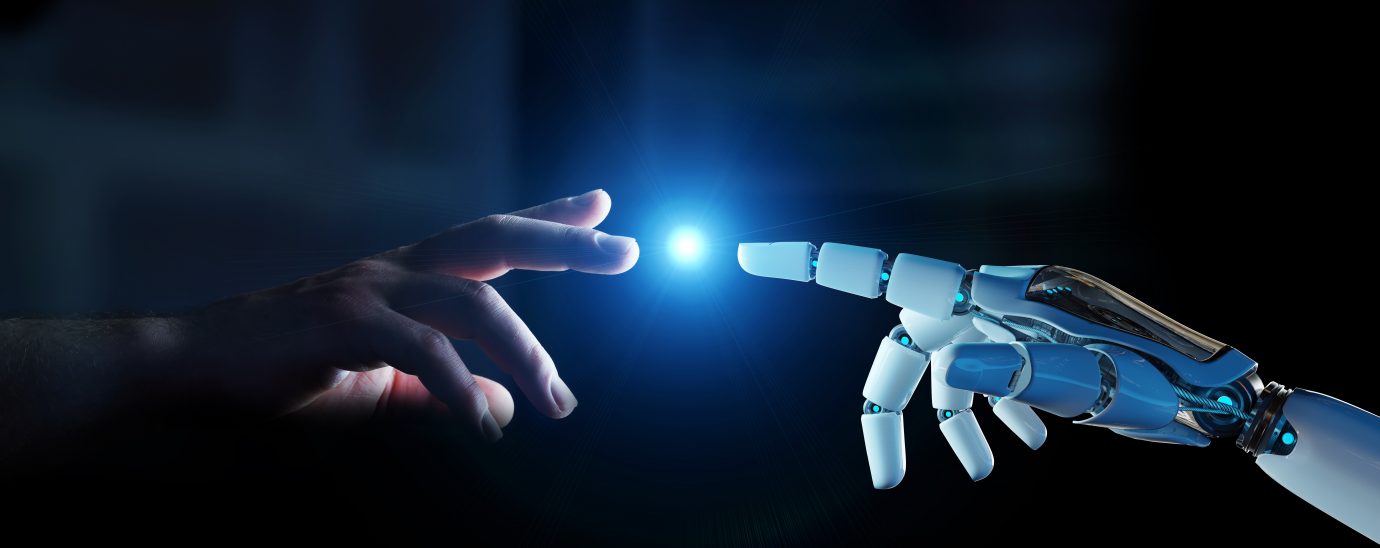
Andy Ray, Sales Director, Vicon, explores the value of cobots in the manufacturing industry.
Many of us will hear the term robot and automatically think of futuristic technologies or the robots seen in many science fiction films. But robots are, in fact, being used across many different industries today, from healthcare, automotive, farming and agriculture and manufacturing.
The increased usage of robots is only set to increase post-COVID as companies look for ways to reduce person-to-person contact. Before the pandemic, the International Federation of Robotics estimated that 1.3 million industrial robots were being used across a wide variety of industries, with a record global average of 113 robotic units per 10,000 employees.
The manufacturing sector, which was one of the first industries to use robots on a massive scale, is currently seeing a significant increase in the use of robotics. According to PwC, more than a half (59%) of manufacturers are already using some form of robotics technology. Robots are proving to be a useful tool for manufacturers, significantly helping to perform core tasks including assembly, distribution, handling raw materials, and product packaging.
The acceleration of digital transformation in manufacturing warehouses means we’re now seeing the implementation of smart warehouse management systems. The ultimate aim is to create a fully autonomous warehouse, where processes are as streamlined and efficient as possible to serve an ever-growing demand for smooth logistics and speedy deliveries.
The use of robots is key to making this vision possible. But although they’re already being used to enhance warehouse operations, we’re now seeing more of a demand for a new generation of robots, called ‘cobots’, a collaborative robot intended for direct human and robot interaction within a shared space. But as robots and humans start to work closely together now, and in the future, it’s crucial both can do so in a safe manner while still being able to achieve the efficiency gains cobots can provide.
Keeping a distance apart
Cobots have typically been small, lightweight machines equipped with sensors to avoid any collision with human workers or any other objects on the shop floor, with the ability to quickly switch off in case of any accidents.
In 2019, more than 18,000 cobots were installed globally, an increase of 11% compared to the previous year. But the success of these early cobots mean there’s now more of a demand for them to complete more complex or heavyweight manufacturing, logistics and material handling tasks. This would require, larger, heavy-duty equipment that’s specifically designed for high-volume and extremely high-accuracy and high-speed production, but this means there’s much more of a higher risk to cobots’ human colleagues.
The key to seamless collaboration
Despite the many benefits of cobots and humans working collaboratively on the shop floor, it’s also, unfortunately, a major engineering challenge. Technologies like motion capture, however, play a key role in helping to overcome this and ensure that both cobots and humans can work seamlessly yet safely together without the risk of potential injury.
Motion capture, which is used across a wide range of industries to digitally record the movement of people or objects, is now being used in manufacturing settings to improve the movement of cobots by tracking drones to analyse the interaction between humans and machines. Access to this data can then be used to identify and avoid any potential obstacles, especially in a space where workers are constantly moving around at speed.
By using technology like motion capture, which can process high volumes of real-time data and deliver speedy response times, drones being used in a manufacturing environment can be trained to react almost immediately to ensure they don’t collide with any human workers or any other objects on the shop floor.
Understanding human activity and drone tracking
Technische Universität (TU) Dortmund, a leading technical university based in Europe has recently carried out extensive research into human activity and recognition and ergonomics in manufacturing.
Through the use of motion capture technology, the university was able to gather visual evidence and data that would provide a deeper understanding of human activity and drone technology. This insight meant TU Dortmund could improve robot control by tracking drones to analyse the interaction between humans and cobots and help the drones identify and stop any potential collisions.
The university carried out a demo where a person in a motion capture suit was able to safely walk through 12 drones flying around the warehouse — highlighting the drone’s ability to react almost immediately and remain at a safe distance to avoid crashing into any obstacles.
The future of cobots
It’s clear that motion capture technology is the key to ensuring cobots and humans can work together collaboratively and safely within warehouses.
While TU Dortmund’s recent research has discovered the value and benefits that motion data capture can bring, it also highlights the fact that there’s a high-level of sophistication needed to make autonomous warehouses a reality.
READ MORE:
- Why human psychology is the key to effective human-robot interaction in the warehouse
- Pepper the robot is coming to SMEs
- Has COVID-19 sparked a rise in robot cleaners?
- Could a robot pick your peaches? How AI could transform global fruit farming
Cobots are already giving manufacturers access to the many benefits of advanced robotic automation without the drawbacks of traditional robots. But as the adoption of cobots continues to increase, it’s crucial that these are built with safety in mind. When every single cobot can work in harmony with humans without any potential risks, there’s no doubt they will become a gamechanger for the manufacturing industry.
For more news from Top Business Tech, don’t forget to subscribe to our daily bulletin!